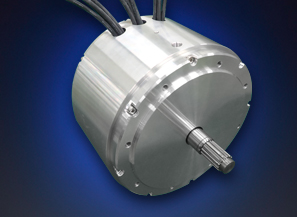
Amorphous Alloy for Motor Core
Amorphous alloy, whose main ingredient is Fe (iron), compared to conventional materials such as silicon steel, has a small no-load loss (iron loss), 1/3 ~ 1/5 that of silicon steel.
It is greatly contributes to energy saving even in motor core applications
Product Catalog Download
Click here to download the product catalog
Contact
Soft Magnetic Materials and Components (for Amorphous Motor)
Topics
Features
The main causes of loss that lowers motor efficiency and causes heat generation are roughly divided into copper loss in the conductor section caused by the drive current and iron loss in the core section caused by the drive voltage. By using an amorphous alloy for the motor core, iron loss can be significantly reduced, and the following effects can be achieved.
- Energy saving by improving motor efficiency
- Reduction of motor heat generation
To quantify the effect, we prototyped a distributed winding IPM motor with a stator physique of Φ215mm × 50mm, evaluated the loss, and compared the motor efficiency. By using amorphous for the stator, iron loss is reduced to about 1/5, motor efficiency is improved by 3% or more, and it has been confirmed motor thermal generation can be reduced by half. In addition, it has been shown that the efficiency improvement in the high rpm range reaches 2% or more even with the amorphous alloy replacement of only the stator teeth in (b) below.
In this result only the core grade is changed under the same structure and the same drive conditions.
With a motor that has been optimized for its structure and drive conditions on the premise of an amorphous alloy, it is possible to achieve ultra-high-speed rotation, which is difficult with conventional materials, and it is possible to reduce the size and to increase the output of the motor.
Iron loss evaluation result
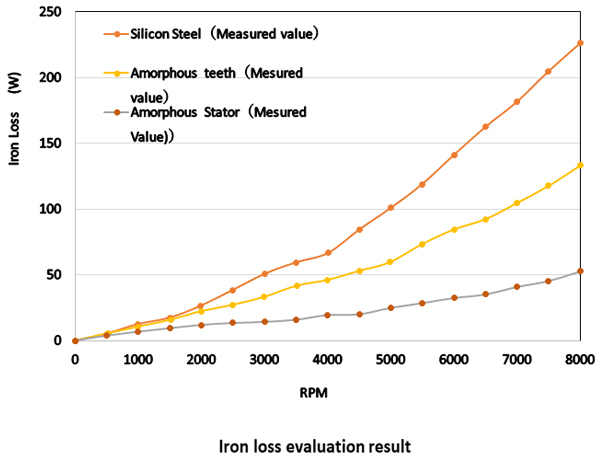
Efficiency comparison
Stator
Rotor
Silicon Steel (gray area)
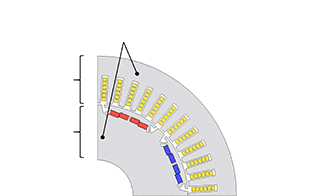
Amorphous (pink area)
Silicon Steel
(gray area)
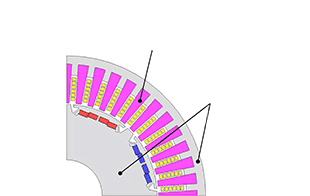
Amorphous (pink area)
Silicon Steel
(gray area)
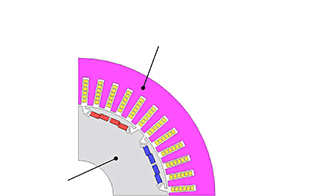
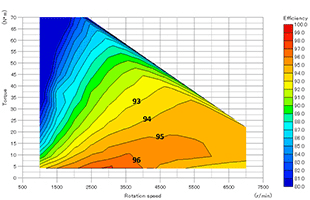
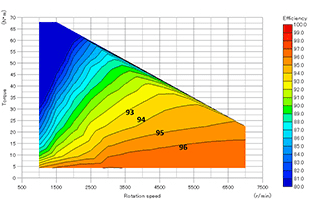
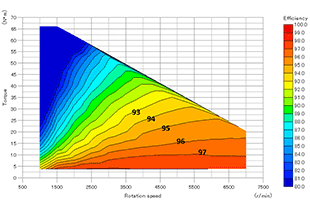
References
Y.Enomoto et al. : " Evaluation of a Motor with an Amorphous Iron Core Punched by a Die", IEEJ Journal of Industry Application vol.10No.6 pp.785-792 (2021)
Product Catalog Download
Click here to download the product catalog
Contact
Soft Magnetic Materials and Components (for Amorphous Motor)
ABOUT US
Leading sustainability by high performance
768,6
billion
18,877