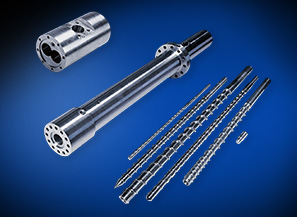
H-ALOY™ Cylinders and YPT™ Screws for Plastic Molding Machines
For instance, the high speed and high pressure injection molding developments for thinner wall products going on, the demand for high performance cylinders and screws has been increasing to endure in severe condition such as high injection pressure exceeded 400MPa under over 350℃ molding temperature.
We have been engaging in high-grade cylinders and screws manufacturing more than 40 years, each aggregate shipment has achieved over 200,000 pieces, and are proud of a leading company in this field.
We will continue to devote ourselves to technology innovation and provide high quality products to support for evolving plastic molding machines such as electric injection machine as ever.
Roll Business Unit
High strength and High pressure resistance NEOC Cylinder Series
Our high-performance cylinders have a structure of hollow backing metal with our original inlay alloy material, which has a strong metal-to-metal bond in boundaries. Picture-1 shows a cutting model to see the structure.
NEOC cylinder series, which has several material types of inlay and features high pressure resistance by new developed high strength backing metal, has acquired customer's favorable reputation since its successive release of several materials. The representative NEOC600 among them has high strength in both inlay and backing metal, which realizes great high pressure resistance. Fig.1 shows the comparison of pressure resistance performance between the case of NEOC600 cylinder alone and the case of NEOC600 cylinder with sleeve shrink fit structure.
Table 1. Comparison of Mechanical properties between NEOC600 and NEOC1000 | ||||||
---|---|---|---|---|---|---|
Material | Inlay Alloy | Backing Metal | Hardness | Bending Strength of Inlay (MPa) |
Proof Stress of Backing Metal (MPa) |
|
Inlay (HRC) | Backing Metal (HS) | |||||
NEOC600 | Ni Base | *HPS700 | 50-60 | 38-42 | 930-1030 | 550-630 |
NEOC1000 | Ni Base +Hard Particles |
*HPS700 | 57-66 | 42-48 | 700-900 | 620-780 |
SCM440 | 57-66 | 28-40 | 340-420 |
There are also several kinds of materials such as NEOC100 with inlay alloy Fe base and NEOC400 with inlay alloy Co base. We can also suggest optimum shrink fit cylinder structure of other cylinders as well as NEOC600 Furthermore, we can study for other solutions to meet the customer's requirement of special specifications based on various kinds of technologies we have been abundantly experiencing and accumulating so far. For further details, please feel free to contact us.
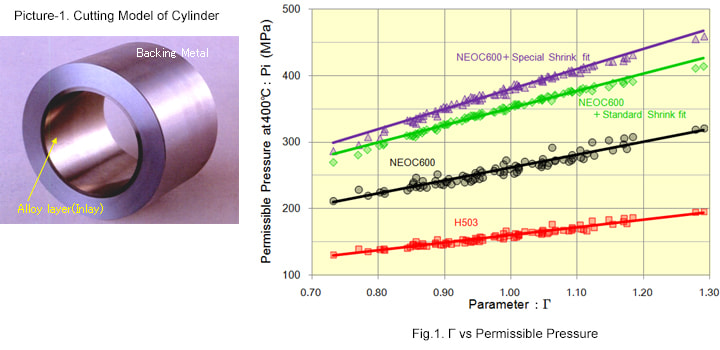
- ※Γ is the parameter value by our own way, which is determined by cylinder's inside diameter and outside diameter.Even if the same Γ, our shrink (standard and special) fit cylinder shows higher permission pressure than the one without shrink fit.
H-ALOYneo Cylinder Series
We have refurbished our long seller H-ALOY™ Cylinder series with the name of H-ALOYneo, which is characterized by adopting new backing material with similar concept of NEOC series. It increases backing metal strength while H-ALOY inlay performance remains unchanged. We believe it makes our cylinders used more widely in the future.
Table 2. Comparison of Mechanical properties between H503 and H503neo | ||||||
---|---|---|---|---|---|---|
Material | Inlay Alloy | Backing Metal | Properties of Backing Metal | Properties of Inlay | ||
Proof Stress (MPa) |
Tensile Strength (MPa) |
Hardness (HRC) |
Bending Strength (MPa) |
|||
H503 | Ni Base | SCM440 | 376 | 778 | 50-60 | 490-590 |
H503neo | Ni Base | Equivalent to ISO 46MnVS6 | 579 | 924 |
We have several kinds of materials such as H305neo and H831neo for Fluorine resin molding. For further details, please feel free to contact us.
YPT™ Screw
We possess the all screw manufacturing process, which consists of material design, raw material manufacturing, heat treatment, machining and final inspection. Optimizing each process ensures to provide high performance screws with stable quality for users. The following is the list of YPT™ screw materials.
Table 3. YPT™ Screw Lineup | |||
---|---|---|---|
Material | Hardness (HRC) |
Feature | Application |
YPT4 | 58±2 | Abrasion&Corrosion Resistance | Middle-Large Size Screw |
YPT42 | 58±2 | Abrasion&Corrosion Resistance High Strength |
Small-Middle Size Screw Screw Tip Set |
YPT71 | 60±2 | High Abrasion&Corrosion Resistance | Molding Plastic with high GF content |
Roll Business Unit
ABOUT US
Leading sustainability by high performance
1,033.2
billion
21,456