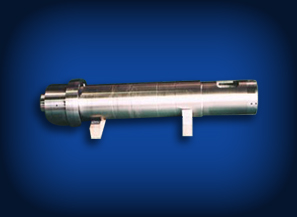
Sialon Ceramics Die-Cast Sleeves
Roll Business Unit
Overview
Sialon die-cast sleeves boast long product life in addition to excellent molten metal heat-retention properties and extrusion stability. These sleeves were first developed in 1986 and they have been steadily improved. In recent years, the use of large-scale sleeves of 2,000 tons-3,000 tons (This tonnage refers to the clamping force of the die cast machine.) has been increasing.
Because automobiles have become lighter to preserve the environment and conserve energy, many auto parts, including engine blocks, have been converted to aluminum. Therefore, aluminum alloy forging has been on the increase. Many of these parts are manufactured using die casting. Although die casting offers the advantage of high productivity, it often causes problems with quality, such as defects in the internal cavity of products and products with chill fracture layers. The task for R&D is to improve these areas.
To improve the quality of die-cast products, a variety of methods to improve forging conditions, starting with molds, have been suggested. However, it has proven very difficult to surpass the molten metal heat-retention properties and extrusion stability offorded by inside the sleeve of conventional die casting. The reason for this is, because the die-cast sleeve is made of steel, the heat energy of the intruded molten metal is greatly leached, and the temperature of the molten metal, especially that which comes into contact with the inside face of the sleeve, is greatly reduced, resulting in potential chill fracture layers. During extrusion, the product is fractured at the tip and chill fracture layers are formed' Athereby resulting in defects. In addition, to prevent seizing between the tip and the sleeve, a large amount of tip lubrication must be used. As a result, a large volume of combustion gas from said lubrication is produced in the internal cavity
Figure 1: Position of Die-cast Sleeve
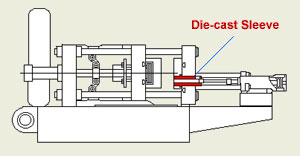
As a result of the above, there is a strong demand in the die-casting industry for sleeves with excellent heat-retention properties and that use little lubrication but feature excellent extrusion stability. For this reason, for some time (since around 1975), the suggestion has been put forth that a ceramic product should be developed for use in die-cast sleeves. For quite some time, this idea could not be put into practice due to the insufficient strength, toughness and heat resistance of ceramics. Finally, Proterial succeeded in developing and put to practical use a die-cast ceramic sleeve by using Sialon, which offers excellent strength, toughness and heat resistance.
Next, we would like to introduce the form and function (features) of Sialon sleeves.
Structure
Figure 2 shows a an exterior view photo, and Figure 3 shows cross-sectional view. The structure of the sleeve is cylindrical and split into an internal and an external layer. The internal layer is a Sialon cylinder, and the external layer is made of a specialized alloy. The internal Sialon sleeve's functions include heat retention and seizing resistance. The external specialized alloy sleeve serves to protect the Sialon from external forces, such as load. The internal and external sleeves are shrunk to fit together to form one unit.
Figure 2: Photo of a Sialon Sleeve
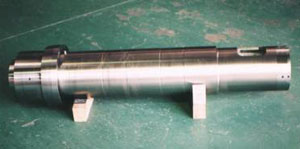
Figure 3: Cross-Sectional View of a Sialon Sleeve
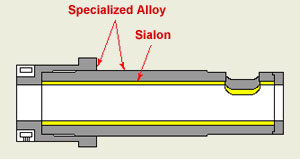
Features
What follows is a comparison of Sialon die-cast sleeves and conventional steel die-cast sleeves.
- 1Superior Molten Metal Heat Retention
Results of both testing and actual application show increased heat retention by 10-40°C and the temperature decrease of the molten metal in the vicinity of the sleeve shows little decrease. As a result, there is lower incidence of the development of chill layers and, therefore, lower incidence of the development of chill fracture layers in the internal cavity of the mold, thereby reducing defective output.
- 2Superior Extrusion Stability
Because Sialon does not react to molten aluminum, there is very little seizure onto the internal face of the sleeve. As a result, there is little sliding drag from the tip, yielding high extrusion stability and allowing a substantial reduction in the volume of lubricant used. In practical application, the volume of lubricant was reduced by 1/5 to 1/2. As a result, the volume of combustion gas produced by the lubricant is reduced, not only reducing defective output caused by the gas but also improving the air quality of the plant.
- 3Long Life
In practical application, Sialon die-cast sleeves were shown to have lifetimes 2-5 times as long as conventional steel sleeves.
Sialon Parts for Handling Molten Aluminum
Thermocouple Protection Tube for Measurement of Aluminum Temperature
Figure 1: Sialon protection tube-single pieces
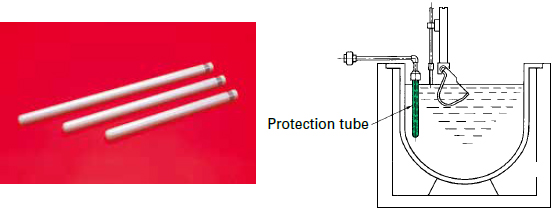
Standard Size(mm)
Outer Diameter | Inner Diameter | Length |
---|---|---|
11.5 | 6.5 | 500 |
15 | 9 | 800 |
22 | 14 | 1,100 |
28 | 16 | 1,100 |
32 | 20 | 1,100 |
34 | 20 | 1,900 |
Stalk for Low-Pressure Casting Machines
We offer a line-up of stalks and thermocouple protection tubes, as Sialon parts for lowpressure casting machines.
Also, we are attempting to create a good seal against air leakage by making use of a composite metal and Sialon structure so as to maintain the required die load and prevent breakage.
- Sizes available
- Outer diameter (mm) : Max 234 dia.
Length (mm) : Max 1,400
Figure 2: Stalk
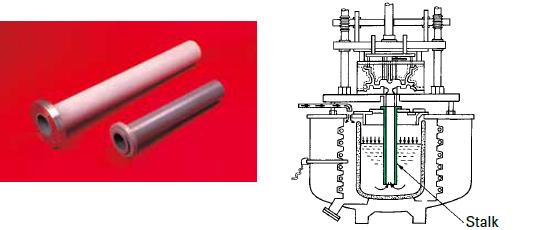
Immersion Heater Tube for Holding Furnaces
Especially useful for disposition of Na fluxes. Applicable to such heat sources as gas burners and electric heaters.
- Sizes available
- Outer diameter (mm) : Max 300 dia.
Length (mm) : Max 1,600
Figure 3: Heater tube
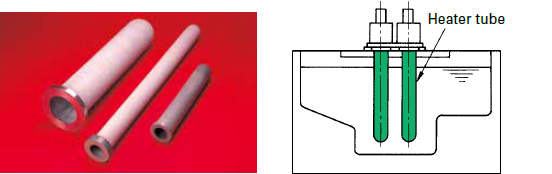
Degassing Rotor for Molten Aluminum
- Sizes available
- Outer diameter (mm) : Max 240 dia
Length (mm) : Max 1,300
Figure 4: Degassing Rotor
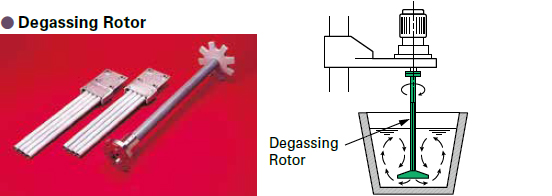
Shot Sleeve for High-Pressure Diecasting Machines
- 1Reduce Cold Flakes ("Cold Flakes") :solidified aluminum defect pieces (scattered structure) formed in shot sleeve
Superior heat-retention. "Possibility of no heating equipment"
- 2Stable shots and longer life (Especially at High temperature ≧ 700℃ or 1290℉)
Less deformation, High corrosion resistance, Erosion resistance and Wear resistance. "Possibility of no water cooling channel"
- 3Energy saving
Sialon's superior heat-retention enables lower molten aluminum casting temperature.
Figure 5: Heat-retention
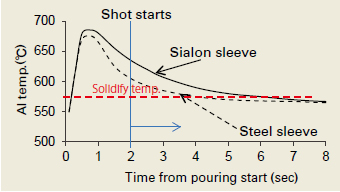
Figure 6: Shot Sleeve (Cut Model)
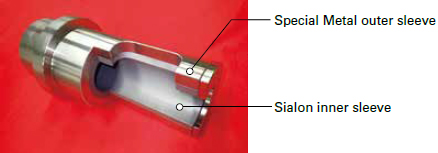
Sialon and Super Sialon
Proterial's Sialon and Super Sialon are ideal for jigs and tools that come into direct contact with molten aluminum on the aluminum melting and casting line.
Proterial has developed this heat-resisting, highstrength ceramic material based on its long experience in processing metals, and has used it in molten aluminumhandling parts.
Features of Sialon and Super Sialon Parts for Handling Molten Aluminum
- 1Little or no contamination of molten aluminum.
- 2Little or no corrosion from molten aluminum.
- 3Little or no adherence of molten aluminum.
- 4High strength remaining intact within the temperature range of molten aluminum.
- 5Two different thermal conductivity
Low thermal conductivity : Sialon is for higher heat retention required parts such as Stalk.
High thermal conductivity : Super Sialon is for higher heat transfer required parts such as Heater Tube
Characteristics of Sialon
Materials | Density (g/cm3) |
4 point Bending strength (MPa) |
Young's modules (GPa) |
Thermal shock resistance (ΔT℃) |
Coefficient of thermal expansion (×10-6/℃) [20~800℃] |
Thermal conductivity (W/m・k) |
Maximum allowable temperature (℃) |
---|---|---|---|---|---|---|---|
Sialon | 3.2 | 750~950 | 290 | 710 | 3.0 | 17 | 1,250 |
Super Sialon | 3.2 | 800~1050 | 300 | 750~1000 | 3.0 | 65 | 1,250 |
Sialon and Super Sialon are used primarily for the production of parts that come into contact with molten aluminum.
The characteristics of Sialon are given below in comparison with those of structural ceramics.
Figure 7: High-temperature strength
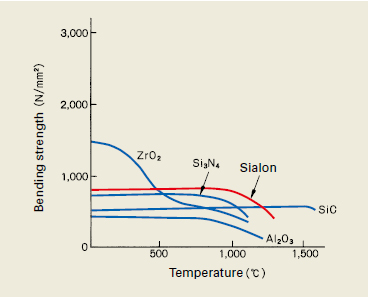
Figure 8: Thermal shock resistance
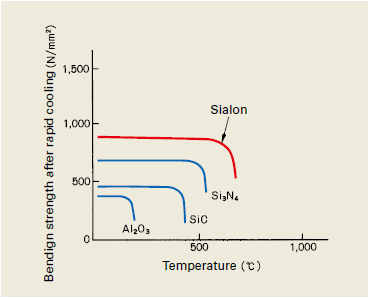
The data in our report do not constitute any kind of warranty or guarantee.
Roll Business Unit
ABOUT US
Leading sustainability by high performance
1,033.2
billion
21,456