Quality-assurance Activities
Quality Assurance Activities
In response to the inappropriate numerical values stated in an inspection report announced on April 27, 2020 (“quality compliance problem”), we have devised measures to prevent recurrence of such a problem as a top priority and are doing our utmost to implement those measures so that such a problem will never happen again.
Based on the recognition that quality is an important management issue for the Proterial Group to enhance its corporate value and achieve sustainable growth over the medium to long term, the Group has set Quality as a Strong Point as one of our six material issues. Aiming to provide our customers with a stable supply of highquality products, we will work together to thoroughly implement measures to prevent recurrence of quality compliance problems and to make quality a strength of our Group that differentiates us from our competitors.
Establishment of the Quality Committee

On April 1, 2023, we established a new Quality Committee consisting of two external experts and the Chief Quality Officer (CQO). Prior to that, the Quality Compliance Committee (active from April 1, 2021 to March 31, 2023) had been responsible for implementing recurrence prevention measures and verifying their effectiveness, etc., however, the Quality Committee was established in order to take over these activities and to add “offering guidance and advice from an expert standpoint on overall quality activities” to its activities.
The activities of the Quality Committee are intended to conduct assessments from an objective perspective regarding the Group’s overall quality activities, including quality compliance activities, and also create mechanisms and management to prevent the recurrence of quality compliance problems, build corporate culture, and revitalize quality-control and quality-assurance activities.
Specifically, the Corporate Quality Assurance Division coordinates activities to prevent the recurrence of quality compliance problems, in addition to quality control and quality assurance activities, and reports to the Quality Committee, which provides guidance and advice on the Company’s activities.
Quality-compliance education
The Proterial Group designates April as Quality Compliance Month and April 27 as Quality Compliance Day every year, and in conjunction with Quality Month in November, which is a nationwide initiative, we take these opportunities to reaffirm our commitment to quality activities by all employees.
Previously, Quality Month was only a domestic initiative, however, we added overseas bases to the scope of the initiative from FY2023, and we have been promoting quality compliance education as a global activity. In FY2023, we conducted video-based education on the themes of “Putting Sincerity into Action” (April) and “Making Quality Our Strength (Importance of Strengthening the QMS)” (November). In order to evaluate the effectiveness of the education, we continuously monitor the level of understanding through questionnaires to the participants, and analyze the opinions of the participants, the results of which are reported to the Quality Committee and the Executive Committee. We will continue to revise content to make it more effective, and will implement education in a way that raises the awareness of quality compliance.
Changing the Corporate Culture and Attitudes to Focus on Quality
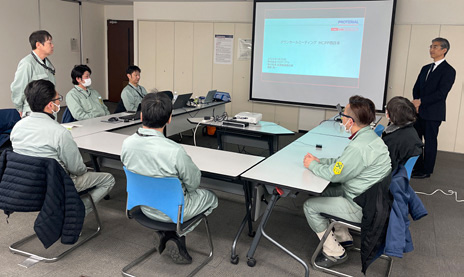
To enhance our employees’ understanding of quality compliance and ensure the effectiveness of reform, the CEO, CQO, and other layers of management send out messages on quality compliance and hold town-hall style meetings on quality on an ongoing basis. The purpose of the town-hall style meetings is to share the importance of quality compliance and acting with sincerity, as well as to listen to the problems and concerns directly from the front line, and to plan and implement solutions by involving the relevant parties in the resolution of these.
Securing the inspection system
Securing the inspection system means establishing a system that automatically imports measured values from measurement equipment to a PC, automatically determines whether a product passes or fails on the basis of that measurement data, and automatically prepares a report to be submitted to the customer.
That automated system is in stark contrast to the conventional one that involves human intervention such as writing the measured values on a special form by hand or entering them into a PC during the inspection process. Moreover, it eliminates the need to write down the measured values and the occurrence of operational errors such as incorrectly writing or mis-typing the measured values. It also improves inspection efficiency by eliminating the need to write down the measured values on special paper or input them into a computer.
We have been systematically working to upgrade and modify measurement equipment at each site, and plan to complete the introduction of these measurement equipment during FY2024 with the intention of finishing data input by the first half of FY2025.
Furthermore, we will also build a system to store images and videos as digital evidence for inspections where data cannot be obtained, such as in the case of visual inspections, and use this as a check against inappropriate behavior, in order to reduce the risk of quality compliance problems occurring.

Holding International QA Meeting
The Proterial Group has organized the International QA Meeting since November 2021 for the purpose of stimulating communication, sharing information and best practices related to quality assurance and quality control, and discussing the establishment of a globally unified QMS system. These meetings are attended by the qualityassurance managers from Group companies around the world and by employees involved in quality assurance in Japan.
The fifth International QA Meeting, held in January 2024, was divided into three regions: Southeast Asia and South Asia, East Asia, and North and Central America. Six case studies were shared and discussed, including on the quality assurance activities being promoted at each site as well as process improvements. We will continue to hold the International QA Meeting as a forum for global dialog on quality with the aim of invigorating the quality activities of the entire Proterial Group.
Establishment of the Quality Help Desk
In June 2022, we established the Quality Help Desk, which allows employees to discuss their concerns regarding quality within the company with peace of mind. The Quality Assurance Unit, serves as the contact point for employees that still find it difficult to make a decision even after repeated dialog and consultation at their workplace. Moreover, the Help Desk will enhance the understanding of quality activities within the Proterial Group by offering advice and by working to solve problems.