Developing a Higher-Efficiency Motor Technology
Using Amorphous Metals
October 24, 2018
Hitachi Metals, Ltd.
Hitachi Metals, Ltd. ("Hitachi Metals") has successfully developed a motor core structure whereby amorphous metals known as Metglas™ are used for part of the motor core to achieve a higher rate of efficiency. The prototype motor produced using this structure was able to achieve efficiency at the IE5*1 class level (97.2%). We will promote R&D with an eye to applying this technology to motors for driving EV*2 and propose new applications of materials for motors along with verification data.
1. Background
Hitachi Metals is engaged in the business of key materials essential for motors, such as, notably, NEOMAX®-a neodymium magnet with a magnetic force of the world's highest class-as well as surge-resistant enamelled wires, amorphous magnetic materials for motors, and motor housings. These materials are used by customers both in Japan and abroad, mainly in automotive, industrial, and home electrical appliance.
With the increase in environmental consciousness in recent years, the demand for smaller, lighter, and more efficient motors is increasing not only in automotive-related markets but also industrial infrastructure- and electronics-related markets. One of the means to achieve higher efficiency in motors is the use of amorphous metals for cores, the core loss of which is as low as 1/10 or less that of magnetic steel sheets. However, amorphous metals are harder to process than magnetic steel sheets, which has conventionally posed a problem for productivity when they are processed into complicated shapes. Against this background, Hitachi Metals has successfully developed a motor core structure that is viable for mass production and can achieve a higher level of efficiency.
2. Outline
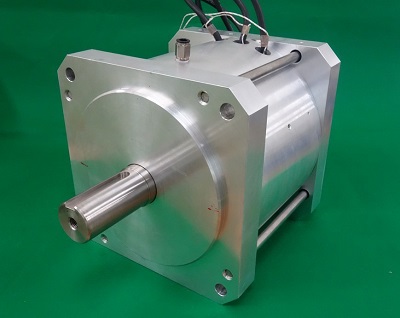
In the motor core structure recently developed, amorphous metals dubbed Metglas™ were used for part of the core. To be more specific, a structure whereby a core with a low core loss would be relatively easy to manufacture was studied and verified by laminating sheared Metglas™ amorphous metals and applying them only to the part of the core called the teeth.
A prototype motor (rated output power: 11 kW, φ215 mm [outer diameter] × 80 mm [stack length]) was also produced using various motor materials belonging to the Hitachi Metals Group, including not only Metglas™ but also HIDENSE™ ultra-high density isotropic bonded-magnets and enamelled wires. Evaluation of the prototype confirmed that a motor efficiency of 97.2%-high enough to meet IE5, the highest level in the guideline for motor energy efficiency-could obtained.
In addition, the prototype motor produced is a radial gap motor*3, the most common type distributed in the market, allowing the use of the stator coil structure, which can be produced using existing manufacturing technology.
We will promote R&D with an eye to applying this technology to motors for driving xEV and propose new applications of the material for motors together with verification data.
Media inquiries: Corporate Communications, Hitachi Metals, Ltd.
hmcc.sa@hitachi-metals.com
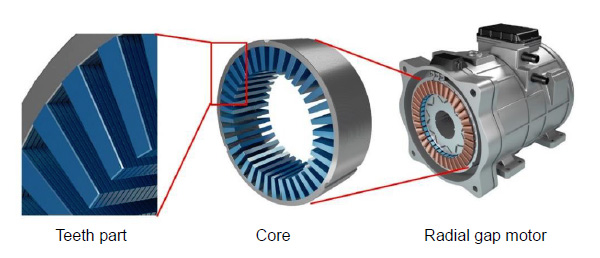
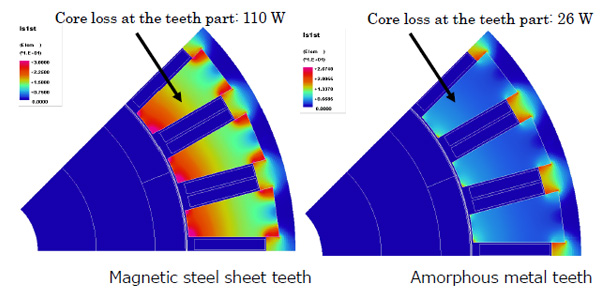
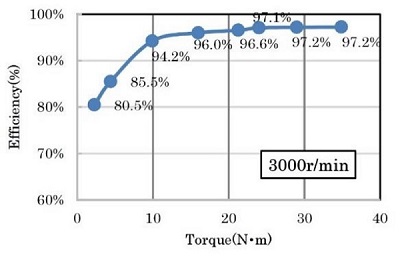
- *1Highest level in the guideline for motor energy efficiency currently under discussion for establishment in IEC60034-30-2 of the International Electrotechnical Commission (IEC)
- *2Including term for hybrid electric vehicles (HEV) and plug-in hybrid electric vehicles (PHEV)
- *3A motor with a structure whereby an air gap (gap between the stator and the rotor) is provided in the radial direction with respect to the rotational axis of the rotor