リチウムイオン電池の正極材製造時CO2排出量を20%以上削減する技術を開発
株式会社プロテリアル
株式会社プロテリアル(以下プロテリアル)は、リチウムイオン電池(以下、LIB)の正極材製造において、これまで必須であった、ニッケルを水酸化ニッケル(Ni(OH)2)化して出発原料である前駆体を製造する工程を経ずに正極材を製造できる技術(以下、本開発技術)を開発しました。本開発技術により、当社が確立した固相反応法(2022年5月公表)に基づく製法(以下、従来製法)と比べて、正極材製造時のCO2排出量を20%以上削減することが可能となります。本開発技術を製品ライフサイクルにわたる脱炭素ソリューションとして電池業界に提供することで、LIBの環境価値向上に貢献していきます。
1.背景
脱炭素社会の実現に向けて、車両走行時にCO2を排出しないEV(電気自動車)に必要不可欠なLIBの需要が急速に拡大することが予想されます。しかしながら、EV車両製造プロセスにおいて、LIB製造はCO2排出量の割合が大きく、中でも正極材の出発原料※1に由来するCO2排出量が最大の割合を占めています(図1)。特に、ニッケル(Ni)から前駆体(水酸化ニッケル(Ni(OH)2))を得る工程で多くのCO2を排出します。
また、欧州では走行時のCO2排出量規制だけでなく、EVのライフサイクル全体におけるCO2排出量規制が今後計画されており、正極材製造をはじめEV車両製造時の排出量抑制が求められています(図2)。
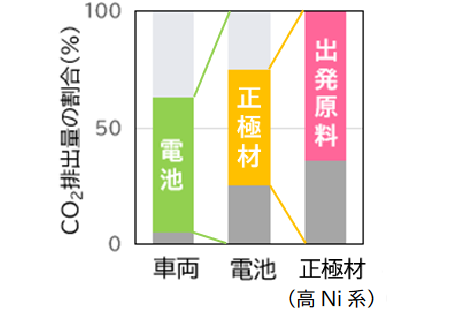
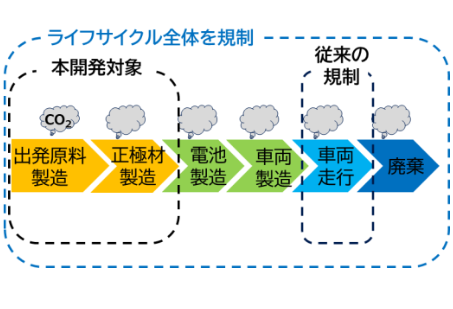
2.概要
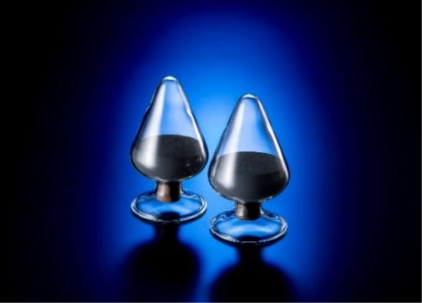
プロテリアルは、正極材の製法として水溶性物質以外を使用できる固相反応法※3を用いることで、出発原料の選択肢を増やせること(2022年5月発表)に着目し、CO2排出量削減につながる正極材製造技術の開発を行いました。その結果、金属であるニッケル(Ni)から一旦、硫酸ニッケル(NiSO4)を製造し、そこからさらに前駆体(水酸化ニッケル(Ni(OH)2))を製造するという、出発原料製造工程を経ず(図3)に、電気化学特性が同等(表)の正極材を製造する技術を開発しました。本開発技術により、従来製法と比べて、出発原料由来のCO2排出量を30%超削減することに成功しました(図4)。これは、出発原料製造を含む正極材製造プロセス全体における※4CO2排出量を20%以上削減することに相当します。
今後は、本開発技術を正極材の量産およびLIBの開発を手掛けるお客様へ、製品ライフサイクルにわたる脱炭素ソリューションとして展開していきます。なお、本技術は5月23日からドイツのシュトゥットガルトで開催される「The Battery Show Europe」に出展します。
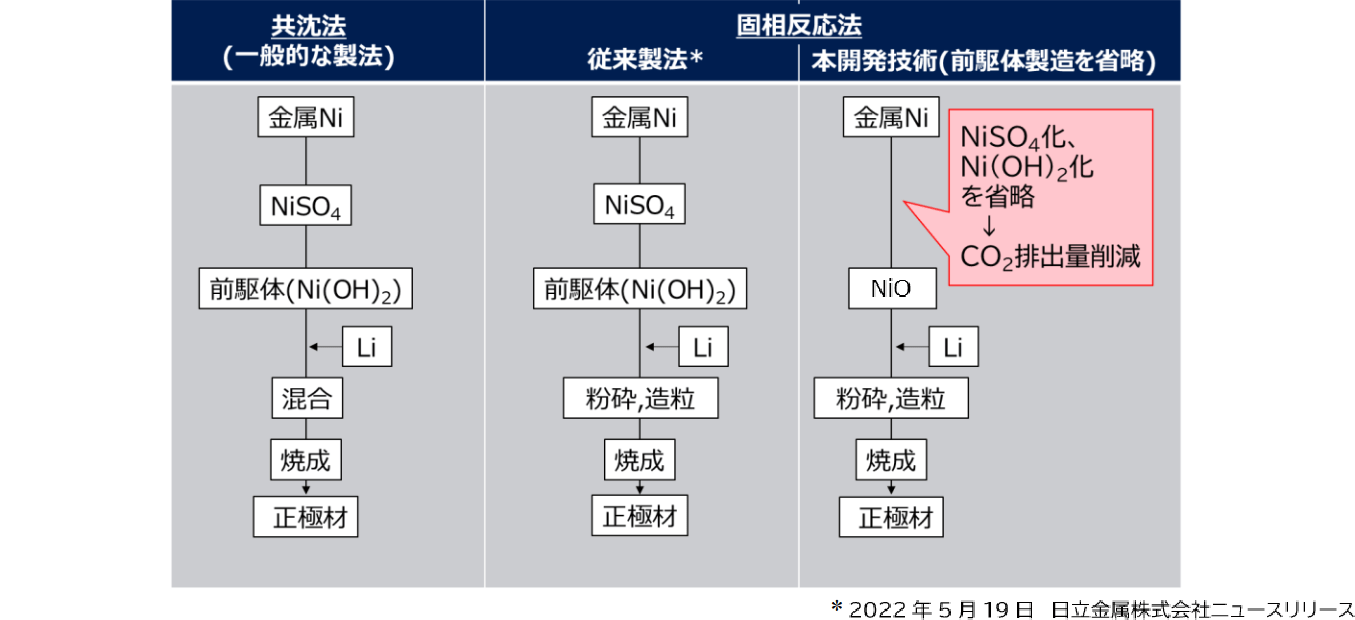
固相反応法 | 初期容量(Ah/kg) | 容量維持率(%) |
---|---|---|
本開発技術(前駆体製造を省略) | 192 | 90 |
従来製法 | 190 | 88 |
初期容量測定条件:対極Li、4.3-2.5V、0.2C(25℃)
サイクル条件:対極Li、4.3-2.5V、1C(25℃)
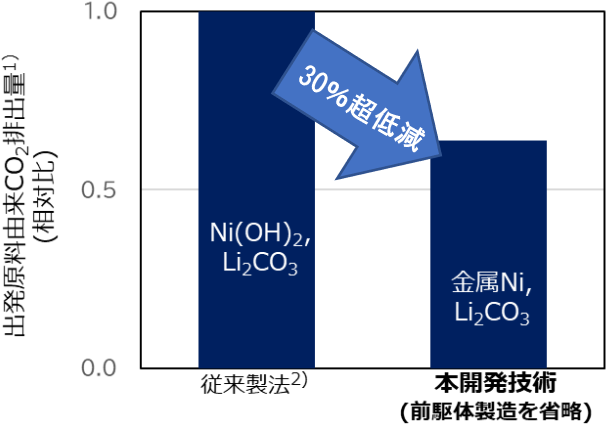
- 1LiNiO2製造に使用する原材料由来のCO2排出量を歩留100%の条件で試算。
CO2排出量原単位には下記データベース、文献の値を使用。
Ni,Li2CO3: LCI データベース IDEA version 2.3
Ni(OH)2: Batteries 2019, 5, 48 - 22022年5月19日日立金属株式会社ニュースリリースリチウムイオン電池向けに温室効果ガス排出量削減に貢献する正極材技術を開発
- ※1化合物(正極材)の生成時に最初の化学反応で必要な出発点となる原料のこと。
- ※2IEA Global EV Outlook 2020、Sustainable Materials and Technologies 32(2022)e00415をもとにプロテリアルにて作成。
- ※3粉末冶金技術をベースにしている製法で、構成元素のリチウムや金属を含む原料粉末を粉砕混合して造粒後に焼成して反応させる方法。対する一般的な製法である共沈法は、粉砕混合や造粒はせず、前駆体と呼ばれる金属の水酸化物粒子を化学的に合成した後、リチウム原料粉と混合して焼成する。
- ※4出発原料由来のCO2排出量と正極材製造プロセスで排出されるCO2排出量の合計
以上
【お客様からのお問い合わせ】
株式会社プロテリアル グローバル技術革新センター 中林 電話 0857-53-6005
【報道機関からのお問い合わせ】
株式会社プロテリアル コミュニケーション部 車谷 電話 080-2108-0159