表面処理の基礎知識!|金型向けに効果的な種類と特長を解説
2023年9月29日
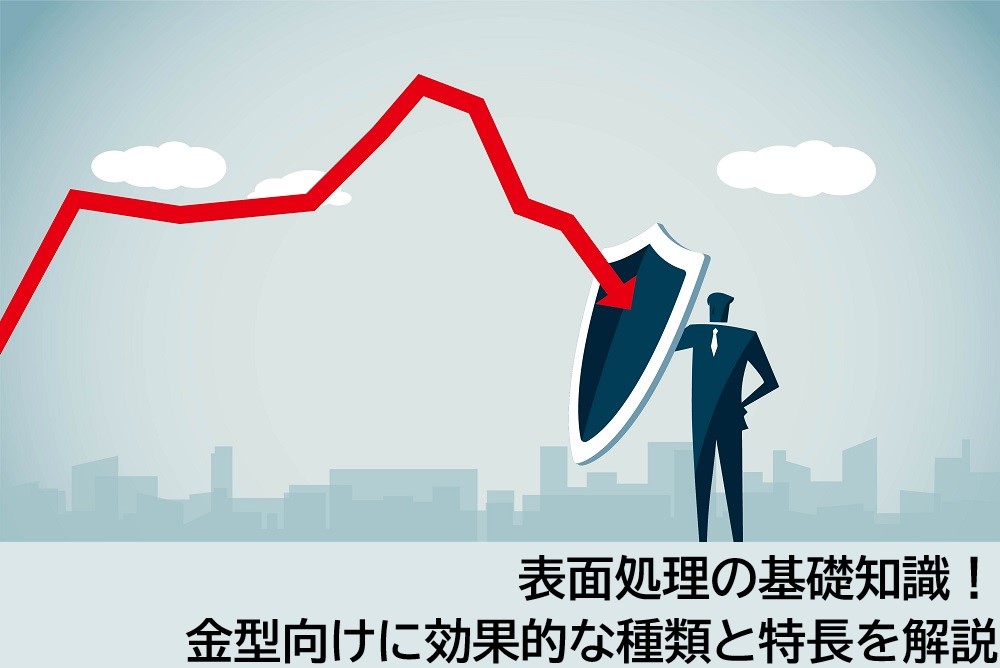
金型の耐久性向上や離型性向上を目的として、金型に表面処理が施されます。
しかし、表面処理にはさまざまな種類があり、金型の用途、材質、目的にあわせて、効果的な表面処理を選択することが重要です。
目的にあった表面処理を選択するためには、各表面処理の特徴や効果と、金型の種類ごとに生じる課題を把握する必要があります。
この記事では、金型に適用される表面処理の特徴や金型の種類別に効果的な表面処理について解説します。
金型の耐久性や離型性などの課題を抱えている場合には、ぜひ一度ご確認ください。
1.表面処理とは?
表面処理とは、被加工材の表面を加工することで新たな特性の付与や強化を実現する加工法です。日常生活においては、フライパンの付着防止や雨具の撥水処理、食器の美観向上などが表面処理によって実現しています。
金型においては、耐久性や耐摩耗性、潤滑性、離型性の向上が主な目的となります。
表面処理を実施する目的
金型に表面処理を施す目的は、使用条件に適用できるように金型の表面を改善したり、新たな特性を付与したりすることにあります。例えば、耐摩耗性、摺動性、離型性、耐熱性、耐食性の向上などが、金型へ表面処理を施す重要な目的として知られています。
表面処理にはさまざまな種類があり、実現したい特性の改善・付与に応じた表面処理手法の使い分けが必要です。
2.金型に適用される表面処理加工の種類と特徴
表面処理の種類は、処理する対象や目的によって多岐にわたります。金型向けの表面処理は、「表面改質」と「コーティング」の2種類に分類でき、さらに窒化、酸化、めっき、PVDなどに分類できます。
表面改質
表面改質は、金型の表面の状態を変化させる加工です。具体的な加工方法には、焼入れや窒化、TRD処理(TD処理)、酸化、ショットピーニングなどがあります。
窒化
窒化処理は、被加工材の表面から窒素原子を内部に拡散浸透させることで、表面を改質する技術です。窒化処理に用いる処理源の違いから、ガス法、プラズマ法、塩浴法、固体媒体法に分類できます。
窒化処理では焼入れや焼戻しが不要であり、高温への加熱による形状変化を考慮する必要がありません。そこで、高い寸法精度が求められる場合に多く用いられます。
また、窒化処理は耐摩耗性に優れ、ガスなどの処理源が届く範囲であれば小さな隙間でも比較的容易に処理できる点がメリットです。
酸化
酸化処理は、被加工材の表面を酸化させる表面処理手法です。
例えば鉄の酸化処理では、構造が緻密で安定した状態であるマグネタイト層の生成が重要です。そこで、ガス比や温度などの条件を細かく調整する必要があります。また、アルミニウムの表面処理として有名なアルマイト処理も、酸化処理に分類されます。表面を酸化させる手法はさまざまですが、特に炭酸ガスや水蒸気を使用するものが一般的です。
TRD処理(TD処理)
TRD処理(Thermo-Reactive Deposition and Diffusion/熱反応析出拡散法)は、バナジウムを含む塩浴中に被加工物を浸漬することで、炭化物層(VC)被膜を生成させる表面処理です。別名、TD処理とも呼ばれます。バナジウムと被加工材である金型材中の炭素の結合により処理が実施されます。
処理膜が強固に結合していることから、耐摩耗性や膜の耐圧強度に優れています。
一方で、高温で処理する必要があるため熱による大きなひずみが発生しやすく、狙い通りの寸法を実現するためにはある程度の経験が必要です。
ショットピーニング
ショットピーニングは、投射材とよばれる粒状物を空気圧や遠心力で投射して被加工物にぶつけて加工する表面処理です。被加工材の表面に、圧縮残留応力の付与や塑性変形、加工硬化、組織変態、表面層改質などを与え、表面特性を改善します。
投射材の種類はさまざまであり、鉄系、非鉄系、ガラス系、セラミック系などに分類されます。また、投射材のサイズは数十マイクロメートルから数ミリメートル程度です。被加工材の材質やショットピーニングの処理をする目的によって適切な種類・サイズの投射材を選定します。
金型向けには窒化処理とショットピーニングを組み合わせることで、ガス軟窒化のみを施す場合よりも、大きな表面処理効果が得られます。
コーティング
金属加工におけるコーティングとは、母材の表面に被膜を作ることです。コーティングは主に、湿式(めっき)と乾式(蒸着)に分類されます。乾式はさらに溶射、CVD(化学蒸着法)、PVD(物理蒸着法)に分類されます。ここでは代表的な表面処理として、めっき、PVD、CVDを紹介します。
めっき
めっきは、被加工物の表面を薄い金属で覆う加工法で、日常生活に欠かせない電化製品に用いられている電子部品に多く用いられています。めっきは、加工方法の違いから、電気めっきと化学めっきに分類できます。
金型にめっき処理をする目的は、表面の硬化や耐摩耗性の向上、耐摺動性の向上が挙げられます。めっきは、100℃以下で加工できるためコーティングのなかでも処理温度が低く、加工時に被加工材の劣化や変形が少ない点がメリットです。
被加工材の耐熱性の観点から、低温での加工が必要な場合には、めっき処理が優先的に選定されます。
PVD
PVD(Physical Vapor Deposition)では、真空中でチタンやクロムをベースとした金属を被加工材の表面に物理的に付着させることで、コーティングを形成します。
PVDはコーティングする際の処理方法の違いから真空蒸着、イオンプレーティング、スパッタリングに分類されます。
イオンプレーティングは、真空中でコーティングの材料となる金属材料を加熱、蒸発させる処理です。発生した金属の粒子をプラズマ中でイオン化することで、被加工材に付着させ、コーティングを生成します。イオン化率が高いため、膜の密着性に優れます。
スパッタリングは、真空中にアルゴンガスを導入し、コーティングの材料となる金属にマイナスの電圧を印加することで、グロー放電を発生させる処理です。プラズマ化したアルゴンイオンが高速でコーティング材料の表面に衝突して粒子(原子・分子)を弾き飛ばし、この粒子が被加工材の表面に付着し堆積することで、薄膜が形成されます。原子レベルで粒子が堆積しているため、表面が平滑で面粗さが低く滑らかな膜が得られます。
PVDのコーティング材料はTi(チタン)が代表的ですが、Ti系やCr(クロム)系など多元系の合金でも成膜が可能なため、目的に応じて多種多様な金属材料が使用されます。
CVD
CVD(Chemical Vapor Deposition)では、成膜したい材料を含んだ原料のガスを、被加工材の表面で化学反応させることでコーティングを形成します。
CVDは化学反応を促進させるためのエネルギーの違いから、3種類に大別されます。熱を与えて分解・反応させる熱CVD法、プラズマのエネルギーで化学反応を促進するプラズマCVD法、光によって分解する光CVD法の3種類に分類され、熱CVDが代表的な手法です。
CVDの化学反応を促進させるためには、コーティング時の処理温度を高温にする必要があります。PVDに比べて高温で処理するため、コーティングの密着性が高い点が特徴的です。一方で、被加工材が熱に弱い場合には適用が難しい点には注意が必要です。
3.金型別:表面処理の目的と効果
金型にはプレス金型、エンプラ(エンジニアリングプラスチック)金型、ダイカスト金型があり、金型の種類ごとに表面処理をする目的は異なります。
金型別に目的と処理方法を確認していきましょう。
ダイカスト金型
ダイカスト金型では、ヒートチェック対策、溶損対策、離型性の向上などを目的に、表面処理を実施します。
ヒートチェック
ヒートチェックとは、加熱・冷却が繰り返し実施される過程で生じる金型表面への亀甲状のひびわれです。ヒートチェック対策を目的とした表面処理には、窒化処理やショットピーニング処理が挙げられます。
窒化処理では、ダイカスト金型表面の硬度を向上させることが可能です。目的に応じて性状を最適化させることで、効果を大きくすることができます。
また、窒化処理に特殊金属を拡散させるショットピーニング処理を組み合わせることで、耐ヒートチェック性の向上に加え、耐焼付き性、耐応力腐食割れ性、摺動性、離型性など、さまざまな特性の付与が期待できます。
溶損
溶損は、ダイカスト金型の鉄と溶湯のアルミの反応によって生成される硬くて脆い化合物の生成と脱落が繰り返す「化学的溶損」と、溶湯の衝突など物理的な衝撃により金型の表面の剥離に至る「物理的溶損」に分類できます。
鋳造加工では、化学的溶損と物理的溶損が複合的に発生することで、金型の損耗が拡大します。化学的溶損の対策としては、金型と溶湯金属との反応抑制が必要です。化合物を有した窒化やコーティング(PVD、CVDなど)処理をおこなうことで、反応抑制を実現します。また、物理的溶損の対策としては、金型表面の硬度や強度の向上が必要です。具体的には、金型材の変更やコーティングなどが対策として挙げられます。
離型性
離型性は、製造した製品をダイカスト金型から外す際の外しやすさの度合です。金型の表面性状や金型の表面に塗布される離型剤の保持性が関係します。離型性を向上するためには、表面改質・コーティングそれぞれの表面処理が効果的です。
離型性向上のためにどのような表面処理を選定するかは、狙いの表面粗さや離型性との複合効果でどのような特徴を持たせたいか、また処理対象の材質やサイズによって決められます。
一種類の表面処理で効果が不十分な場合には、複数の処理を組み合わせることも可能です。例えば、窒化処理にショットピーニングを組み合わせることで、離型剤保持性や摺動性の向上により、離型抵抗が低減する場合があります。
プレス金型
近年は、プレス加工で製造する製品の高強度化や高サイクル加工化により、かじりや凝着が発生し、金型の寿命が低下しやすくなっています。
かじりや凝着などの課題を解決するためには金型表面の高硬度化や摩擦係数低減が必要です。この課題を解決するためTRD処理やCVD、PVDなどの表面処理が用いられます。
しかし、TRD処理やCVDは1,000℃程度の高温で処理する必要があり、寸法の変化や変形などが課題です。そこで近年は、低温の処理で寸法変化や変形が少なく、用途に応じてさまざまな材料のコーティングが開発されているPVDの採用が拡大しています。
かじり
かじりとは、金型と被加工物間の摺動面に凝着が発生すること。また、硬い突起や硬質粒子の切削作用により、金型表面の一部がスジ状に磨耗・脱落することをさします。かじりを抑制するためには、金型表面の硬度を高める対策が効果的で、高硬度が得られるコーティングが対策として適用されます。
凝着
特にアルミニウム合金のプレス加工においては、金型材の鉄とアルミニウムとの高い親和性により凝着が発生することがあります。この凝着は、アルミニウムに対して反応性が低いコーティング膜を金型に施すことで改善します。コーティング膜の種類としては、PVD処理を用いたDLC(Diamond Like Carbon)が適用されることが一般的です。
エンプラ成形金型
近年、軽量化と強度の両立を目的として、エンプラ(エンジニアリングプラスチック)の高性能化が求められています。
金型は、被加工材の硬度や強度が高いと摩耗や腐食による損耗が激しくなるため、高性能化したエンプラを成形する金型には、耐久性向上が必要です。
エンプラ成形金型の耐久性向上には、表面処理が効果的です。特に摩耗や腐食寿命の向上を実現するためには、化合物層を持たない窒化処理が優れています。
4.まとめ
金型の表面処理は、窒化やショットピーニングなどの表面改質、CVDやPVDなどのコーティングに分類できます。金型の損耗状況や課題は要因が多岐にわたるため、要因を的確に把握し解決に適した処理を施すことが重要です。
プロテリアルでは、さまざまな金型材、損耗状況に合わせた最適な表面処理を提案するために、PVDコーティングのTribec(トライベック)をラインナップしています。
Tribecは、さまざまな金型に必要とされる高い摩耗性、優れた潤滑性、耐熱性などを実現した独自のコーティング技術です。複数の材料で構成される層を融合させることで多彩な機能を実現でき、金型のもつ可能性を最大限に引き出せます。
Tribecの種類
Tribecシリーズの主な用途や特徴は以下です。
組成 | 商品名 | 主な用途 | 特徴 | 膜厚※ |
---|---|---|---|---|
バナジウム系 | Tribec炬(かがり) | 高強度鋼板の加工 冷間プレス、ホットスタンプ |
耐カジリ性+耐摩耗性 | 10マイクロメートル以上 |
Tribec炬V(かがりブイ) | メッキ鋼板の加工 冷間プレス、ホットスタンプ |
耐カジリ性+耐凝着性 | 10マイクロメートル以上 | |
クロム系 | Tribec剛(たける) | 汎用 鍛造・プレス ダイカスト |
耐熱性+耐摩耗性 | 8マイクロメートル |
Tribec晃(ひかる) | 汎用 切刃 | 耐熱性+耐摩耗性 | 3マイクロメートル | |
Tribec晃smooth(ひかるスムース) | 精密鍛造 | 表面平滑膜 | 3マイクロメートル | |
炭素系 (水素フリー) |
Tribec極(きわみ) | 非鉄用高精度加工 Al・Niのプレス 樹脂の射出成形 |
高硬度+低摩擦 | 0.3マイクロメートル |
Tribec極Mk-Ⅱ(きわみマークツー) | 0.8マイクロメートル |
※膜厚は目安であり、保証値ではありません
Tribec処理は、金型の用途や材質、損耗の種類、求められる寸法公差によって使い分けられます。実際の金型に生じる損傷は複数の要因が関連している場合があるため、画一的な対処ではなく、損傷の要因を調査し適した表面処理を決める必要があります。
Tribec(トライベック)についてはこちら
プロテリアルでは、適切な表面処理を提案するために目的や課題の要因解析も可能です。
ダイカスト金型の表面処理についてはこちら (㈱プロテリアル特殊鋼サイトへ移動します)
当社の製品に関するご相談やご質問は、お問い合わせフォームよりお気軽にご連絡ください。
- Tribecは株式会社プロテリアルの登録商標です。